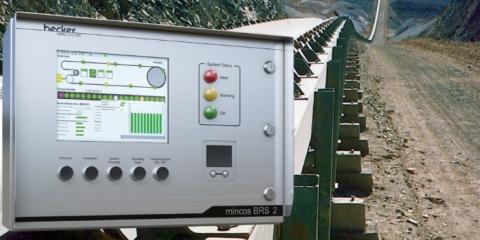
Within the mining industry, conveyor belts play an essential role in moving materials across large distances within mines efficiently, while simultaneously being vulnerable to damage such as rips which could result in downtime and costly repairs if left unaddressed promptly. Implementation of Belt Rip Detection systems can significantly mitigate such risks; in turn ensuring smooth operations. Here, we explore what belt rip detection does, why it matters, and its contributions towards reduced repairs/maintenance costs on conveyor repairs/maintenance costs overall.
Understanding Belt Rip Detection
Belt rip detection is a specialized monitoring system developed to quickly recognize tears, rips and significant wear in conveyor belts as soon as they occur. Utilizing sensors, cameras and other monitoring tools that detect even minute signs of damage quickly allows immediate intervention when damage is discovered - automatically alerting operators or stopping conveyors to prevent further destruction if the detection system detects anything concerning.
Becker Mining USA, an innovative provider of mining solutions, offers cutting-edge belt rip detection technology specifically adapted to meet the rigorous demands of mining operations. This proactive solution offers immediate detection and allows mine operators to address potential issues before they become severe - helping reduce repair costs significantly and avoid extensive repairs down the line.
Mining conveyor belts must withstand extreme conditions on an everyday basis; from heavy loads, abrasive materials, and extreme temperatures to developing rips in their belts which deteriorate further each rotation, leading to substantial costs in repair work and potential safety risks for employees and environmental contamination issues. When this damage goes undetected and worsens with each rotation it could even result in permanent belt rupture, leading to:
Costly Repairs: Without timely detection and intervention, minor tears in conveyor belts may quickly turn into costly repairs or even complete replacement costs, leading to significant repair or even complete system shutdowns and significantly increasing downtime for mining operations. Downtime can occur due to unexpected stoppages that disrupt their entire mining operation and reduce overall output.
Safety Risks: Faulty conveyor belts pose serious safety hazards; belt rip detection helps mitigate against unexpected failures that endanger workers nearby and save costs by early identification of any rips, improving both cost efficiency and increasing worker protection. Eventually these issues could even help ensure improved worker protection overall.
Modern Belt Rip Detection system In order to accurately identify belt rips on conveyor belts, modern belt rip detection systems use multiple technologies. They include:
Magnetic Coil and Loop Systems: When embedded within conveyor belts, magnetic coils generate an electromagnetic field which, when disrupted by tears in the belt material, alerts operators immediately of potential problems.
Ultrasonic Sensors: Ultrasonic sensors monitor the integrity of belt surfaces using ultrasonic waves; changes can indicate signs of tears or significant wear on them.
Optical Cameras: High-speed cameras capture images of the belt in real time and feed them directly into software that detects anomalies associated with rips.
Infrared Sensors: These sensors use infrared technology to measure heat changes on a belt's surface. Rips often create friction that results in heat production that infrared sensors can pick up as an indicator of potential belt damage.
GET IN TOUCH
In a hurry? Call us at 276-285-3841
Belt Rip Detection Is Essential in Reducing Conveyor Repairs
Implementing belt rip detection has proven an asset for mining operations and directly contributes to minimizing conveyor repairs:
Early Detection Saves Repair Costs
A small tear or tear-through on a belt can quickly escalate, often without intervention, into something much larger and costlier to fix later. Early detection allows for prompt action such as simple patching or replacement section to avoid extensive repairs or full belt replacement which would otherwise need to be conducted during scheduled maintenance visits and potentially saves on repair costs considerably.
Mining operations often run to tight schedules, and unexpected conveyor belt failure can halt operations completely. When an automated rip detection system detects problems with conveyor belts, operators can plan repairs during low activity or scheduled downtime periods to minimize disruptions to their process and to minimize downtime for repairs. Furthermore, real time alerts enable quick closure times to reduce disruptions caused by absence from operation of one of their conveyor belts.
Enhances Safety Belt conveyors transport thousands of tons daily. An unexpected failure due to an undetected rip can present serious safety threats for workers on conveyors; belt rip detection systems add another layer of protection by alerting operators before any potential damages become more critical and life-threatening - this feature is especially crucial in mines which prioritize worker safety as a top priority.
Longer Conveyor Belt Lifespan
Conveyor belts can be an expensive investment and the costs associated with replacing them entirely are substantial. By detecting early warning rips in their conveyor belt, operators can take action to repair minor damage before it worsens further and extend its lifespan, ultimately decreasing overall lifecycle costs for conveyors by less repairs/replacement needs and costs associated with repairs/replacements needed in their service lives.
Mining operations can be complex affairs with many interdependent systems and processes at work within them, and conveyor belt downtime affects each step in the mining process from extraction through to processing. Belt rip detection enables operations to maintain productivity levels by keeping materials flowing efficiently without backlogs or delays arising, keeping material flows unobstructed for maximum productivity levels and minimizing downtime costs.
Practical Benefits of Implementing Belt Rip Detection in Mining
Employing belt rip detection can bring tangible advantages to mining operations, including:
Improved Productivity and Decreased Operational Costs
Fewer breakdowns mean improved productivity for companies to meet production goals while simultaneously decreasing operational costs overall. This reduced downtime results in greater production targets being met and ultimately lower operational expenses overall.
Environmental Responsibility
Mining companies can reduce their environmental footprint by increasing conveyor belt lifespan. Fewer replacements mean reduced waste production, helping companies meet sustainability objectives more easily.
Long-Term Savings on Belt Maintenance
Reducing major tears reduces maintenance needs over time and results in long-term cost savings for mining operations.
GET IN TOUCH
In a hurry? Call us at 276-285-3841
Selecting an Appropriate Belt Rip Detection System
Mining companies need to consider several aspects when choosing an effective belt rip detection system:
Type of Materials Transported: Transporting sharp rocks increases the chance of ruptures. Belt Length and Speed: Longer belts require more sensitive detection systems in order to monitor for potential issues.
Environmental Conditions: Mines located in extreme environments require reliable detection systems that can withstand temperature variations without faltering, while integration into current conveyor belt setups should prioritize systems compatible with them so as to ease installation procedures and save time and effort.
Becker Mining USA provides tailored belt rip detection technology solutions tailored to individual mining needs, optimizing the durability and performance of conveyor belts.
Conclusion
Conveyor belts serve as the backbone for material transport, yet their susceptibility to damage makes them extremely vulnerable. Belt rip detection technology has revolutionized how mining firms approach conveyor maintenance by minimizing repairs while optimizing efficiency and effectiveness. By investing in advanced belt rip detection solutions like Becker Mining USA's, mining companies can extend the longevity of their conveyor systems while improving operational safety and decreasing maintenance costs; early rip detection serves not simply as a preventive measure but rather serves to secure their sustainability and efficiency of mining operations operations!
Products We Offer:
- Explosion Proof Equipment
- Transformers
- Arc Guard
- Longwall Electrical Systems
- Capacitor Trip Devices
- Electrical Equipments like capacitor banks, switch houses, junctions, and splice boxes.
Power up your productivity with Becker Mining's ground fault relays - the reliable and efficient solution for all your power distribution needs. Call us today!